| Infor
Los retos para mantenerse competitivos en el sector de alimentos y bebidas luego de la pandemia
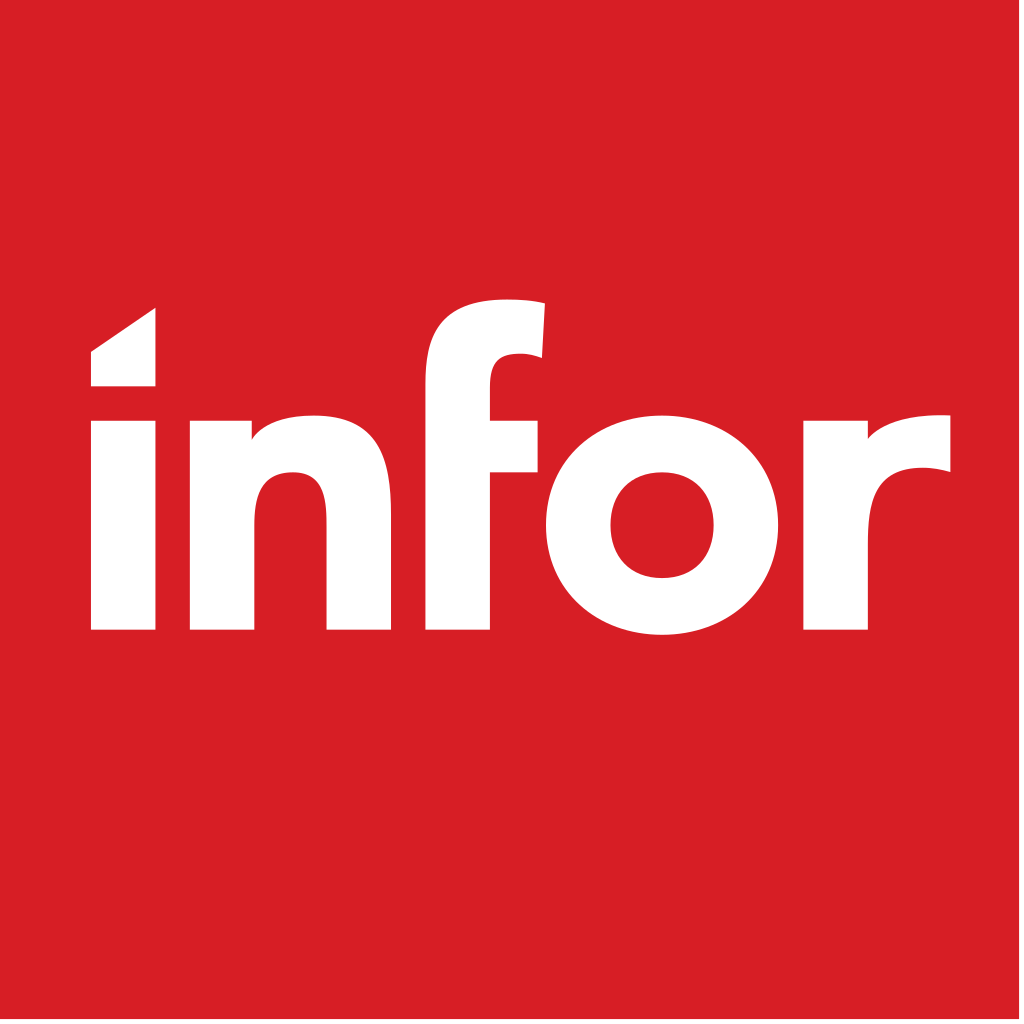
Infor analiza cómo el surgimiento del mantenimiento 4.0 eleva el estándar de seguridad en la industria de alimentos y bebidas.
* Por Nicolás Luders, Solution Consultant de Infor. Link a foto del vocero
La pandemia aumentó los desafíos que afrontan las empresas manufactureras de alimentos y bebidas, la demanda de los consumidores varía, existen cuellos de botellas en la distribución de algunas áreas y suben los costos. Todos elementos ideales para crear la tormenta perfecta. Especialmente, las devoluciones por seguridad siguen representado uno de los mayores desafíos que enfrentan las empresas, ya que son costosos y riesgosos.
Un reporte indica que las devoluciones por seguridad en los alimentos están en constante incremento. Generalmente debido a mayores requisitos en el etiquetado, mayor capacidad para detectar anomalías y el crecimiento en el sector de “libre de”, el cual es vulnerable a temas de contaminación.
Y por supuesto, el Covid que trajo un nuevo foco en el riesgo de contaminación de personas y patógenos dentro de las plantas de producción.
En un mundo donde la seguridad de los alimentos es fundamental, la reputación de la marca es indispensable. Y en cuanto a ocuparse de este tema, la gestión de los activos físicos y el mantenimiento para muchos siguen siendo el área que aún tiene un gran potencial para mejorar.
Maximizando la automatización, minimizando los riesgos
No es ningún secreto que la clave para resolver estos desafíos reside en la transformación digital. Muchas plantas todavía usan procesos manuales centrados en hojas de cálculo, para sus programas de mantenimiento de los equipos, lo que es sumamente riesgoso ya que deja a las empresas de alimentos vulnerables a los errores que puedan ocurrir, expuestas a tiempos de paro y costos innecesarios y procesos largos para cumplimiento de normas.
El nivel de automatización asociada a la producción de alimentos varía enormemente, pero una cosa es clara: cuanto menor es la automatización, mayor es el riesgo de que ocurran errores, lo que pueden causar tiempos de paradas, riesgo en seguridad y mayores desperdicios. Un alto nivel de automatización, machine learning e inteligencia en la adopción de un mantenimiento de activos físicos predictivo o prescriptivo puede disminuir el riesgo considerablemente, minimizando devoluciones y maximizando la reputación y las ganancias.
El reto del big data
Los sensores en todas las máquinas y líneas de producción ayudan a brindar los datos necesarios en tiempo real, brindando la oportunidad para mapear los datos en vivo con información histórica y de terceros y tomar decisiones informadas en forma rápida.
El nivel de granularidad de visibilidad que se puede lograr utilizando los sensores es sumamente valioso. Por ejemplo, en ciertas máquinas, las vibraciones pueden monitorearse para detectar el nivel en que los rodamientos se deforman de redondas a ovaladas, impactando la confiabilidad del equipo y prediciendo el punto en que fallaron.
Pero el objetivo final es mucho mayor que simplemente mejorar el OEE (efectividad total del equipo) en las líneas de producción. Por ejemplo, no es raro escuchar devoluciones por el riesgo de contaminación metálica en los productos. En general, este tipo de devolución es sinónimo de máquinas que fallan y un riesgo teórico de que existan lotes comprometidos. El problema es que la visibilidad de las máquinas se recolecta al final del día, en lugar de en tiempo real, lo que resulta en una demora que rápidamente se traduce en un cuello de botella, con riesgo de la reputación y la logística.
Y en el caso de contaminación potencial por Covid u otros virus o bacterias, una mayor automatización inevitablemente resulta en una necesidad de menos personas en el piso de planta, disminuyendo el riesgo, pero de igual manera puede ayudar en la recolección de datos de los escáneres de temperatura y del reconocimiento de imágenes. Esta información puede ayudar a brindar datos de los operativos desplegando señales de infección y brindan una oportunidad de disminuir el riesgo. Además, el software para el mantenimiento predictivo, pueden identificar los intervalos adecuados de limpieza para minimizar el riesgo de contaminación, y evitar limpieza innecesaria que puede afectar la vida útil de las máquinas.
Al recolectar datos en tiempo real, se pueden predecir las fallas en las funciones, en lugar de esperar al final del día una vez que el daño ya ha ocurrido, el personal puede verdaderamente identificar las anomalías antes de que sean problemas grandes.
Esencialmente todos los sensores del mundo no pueden ayudar a brindar valor, impulsar el performance o disminuir el riesgo si no están conectados y los datos que recolectan se quedan aislados y sin evaluar.
Mantenimiento 4.0
El Mantenimiento 4.0 se ocupa de esta disparidad por medio de la captura de la lectura de los sensores en los depósitos de datos, aplicando algoritmos y analytics para entender precisamente qué activos fallan, e identificar cómo corregir el problema, todo en tiempo real. Este formato aprovecha estos datos para asesorar al personal del mantenimiento sobre las acciones a tomar para evitar el mal funcionamiento de los activos.
El pase del mantenimiento reactivo, que se considera la estrategia más fácil, pero que generalmente es la más cara a largo plazo, a un mantenimiento predictivo basado en la condición de los activos es un cambio crucial en la búsqueda de elevar los estándares y expandir el market share.
Esta capacidad para identificar y resolver los temas en tiempo real garantiza una operación fluida de la planta de producción de alimentos y disminuye el riesgo de desperdicios junto con probables paradas de planta.
Un modelo convergente
La transformación digital es sin duda la convergencia de la tecnología, las operaciones y los negocios para investigar los modelos que son predictivos en lugar de reactivos y minimizar enormemente el riesgo de devoluciones.
Muchos más que OEE, que era normalmente el objetivo final en las soluciones de mantenimiento anteriores, la visibilidad profunda y el análisis sirven para optimizar la confiabilidad y el performance y en conclusión aumentar las normas de seguridad y demostrar las mejores prácticas en todo el sector de alimentos.
Debido a los cambios en el sector de alimentos ocasionados a partir de la pandemia, son pocos los que pueden poner en juego su reputación y los márgenes de ganancia. Las empresas que miran hacia el futuro consideran la estrategia del mantenimiento 4.0 en su búsqueda para proteger tanto a sus clientes como a la reputación de sus empresas.
# # #
Acerca de Infor
Infor es un líder global en software empresarial en la nube especializado por industria. Brinda aplicaciones empresariales para operaciones críticas a 67.000 clientes en más de 175 países, el software de Infor está diseñado para ofrecer mayor valor y menores riesgos con ventajas operacionales sustentables. Nuestros 17000 empleados cuentan con gran experiencia en la industria y utilizan información basada en datos para crear, aprender y rápidamente adaptarse para resolver nuevos retos de la industria. Infor se compromete con sus clientes a brindar herramientas modernas para transformar sus negocios y acelerar su camino hacia la innovación. Más detalles en www.latinamerica.infor.com o www.infor.com.
Contacto de prensa
Muriel Siffre | Ejecutiva de Cuentas PR | msiffre@mazalan.com.ar | (+54 9) 11 61893045
Luisina Fierro | Asistente de cuentas PR | lfierro@mazalan.com.ar | +54 9 (221) 560-5694